English
Chinese
What is InPlane
In the automobile, the surface is defined as the any material in an XY direction. This could be the dash, center console, interior door, headliner steering wheel surface. The cross-sectional thickness is the Z direction. And from a sensing perspective, this is referred to as the stack thickness. The side of the surface that the user touches is often referred to as the A-Surface, and in a sheet of plastic the A-Surface with a thickness, in this example of 2mm would be the stack thickness.
InPlane sensing is the ability to provide sensing input in the thinnest total depth physically possible, in the same plane as that A-surface so the sensor board is in the plane of the A-Surface.
Today’s Sensor Module
Today’s sensor module needs to support the sensing layer and the controller circuitry. In delivering the HMI (Human Machine Interface) experience there is also feedback than can include several types of feedback such as lighting, audio, and haptic, or if a mechanical mechanism mechanical feedback such as from a tact switch.
In automotive lighting applications using traditional lighting methods there is a light pipe framework and the LED blasts light at a distance through the light pipe to achieve the specified brightness to back light a given icon. Intelligent illumination not only lights the touchpoint to inform what function is enabled but when engaged it would show a different color to show it’s engaged.
For example:
- Non-Illuminated = a hidden/ unavailable touchpoint,
- White light = available illuminated touchpoint (ex. Headlight white icon, light is off)
- Green light = enabled function (ex. Headlight green icon, headlights are on)
- Blue light = secondary function (ex high beam headlight blue icon, high beam light is on)
To understand how to enable all these functions with one touchpoint engagement refer to gestures blog. The user experience and final behaviors tie to certain standards and are under the control of the OEM, they are dependent on the selected HMI design components capabilities and the imagination of the interface designer. Some may only need white to identify the button and not opt to provide feedback of current state. If there are multiple touchpoints there may be a need to individually address each touch point and its respective function separately. Not all in-market technologies / solutions can offer individually addressable capabilities.
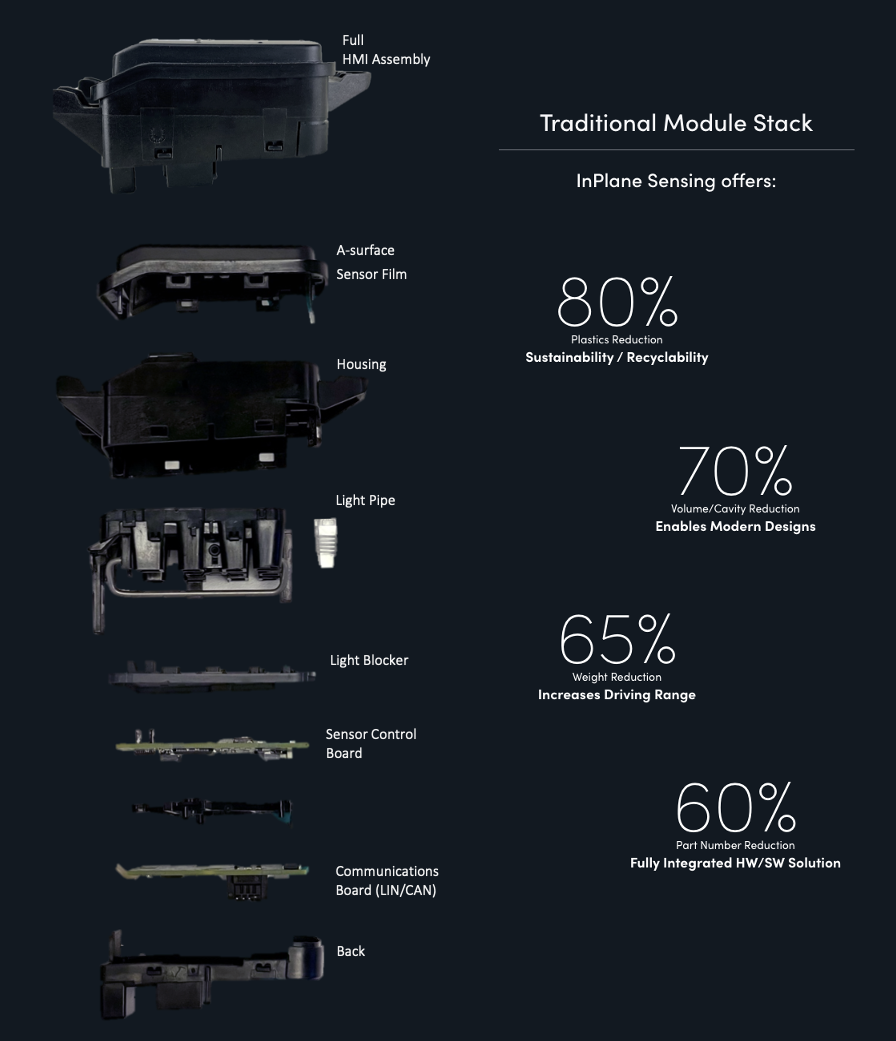
The traditional module has several functional components
- sensing controller (ex. Capacitive controller, feedback controller for lighting,
- processing controller to control the sensors and feedback mechanisms
- feedback controller PWM (Pulse Width Modulator) components for
- lighting effects such as dimming or effect patterns),
- audio speaker components (for example in a steering wheel), and
- haptic controller and haptic motor if a solid state component, and
- the communications board to support connectivity to the rest of the car through common protocols such as LIN or CAN.
For example, with a capacitive technology there is a sensing layer, using materials such as ITO (Indium Tin Oxide) film, FPC Flexible Printed Circuit, or PCB (Printed Circuit Board) that delivers the capacitive trace that laminates to the A-surface and connects to the sensor silicon which is part of a module with supporting electronic components.
Today the most common automotive application is this sensing film layer has been laminated to the back of the A-surface and in a few cases inserted InMold, literally in the molded part.
IME, In Mold Electronics is one form of InPlane, where not just the film but the entire sensing electronics components including the controller are in the molded part.
The InPlane value proposition is that it brings is amazing in many areas and now can offer that in the plane of the A-surface
Take one sample existing module, the exact module and manufacturer is not relevant, likewise the exact measured numbers are relative and will vary for each part, but in this teardown analysis of the production HMI part assembly, the thin-ness comparison to InPlane can’t be overlooked. Reductions in the amount of plastic that results in Sustainability and Recyclability advantage. The total space, the volume cavity is drastically reduced that enables designers to create interacts where previously prohibited.
Imagine a center console stowage cover, InPlane could fit where a traditional assembly could not even consider fitting enabling new application that were previously not an option. When implemented throughout the vehicle, just like in automotive wiring, a network protocol delivers drastic weight savings, like the transition to networked wiring, this offers the same weight savings that adds up to increasing driving range, which ultimately is a measure that hits the bottom line for car buyers.
InPlane is a single planar thin module that can also be the surface for the other desired components beyond sensing such as an MCU, feedback that could include lighting, speaker or haptic motors and the communications board.
InPlane Sensing HMI is the ability to offer all the components the primary sensing, processing, feedback, communications all “in plane.”
Reimagine with InPlane
Now reimagine that what has been done in the past with todays advanced technology capabilities. OEMs can rethink the way of the past and get the same benefits in less space. With integration of the key components that can be integrated into one tiny component(s) this is now becoming a reality. InPlane Sensing and InPlane HMI (sensing plus integrated control, processing, feedback, and communications) is the method for OEM (and Tier1s) to deliver this new experience.
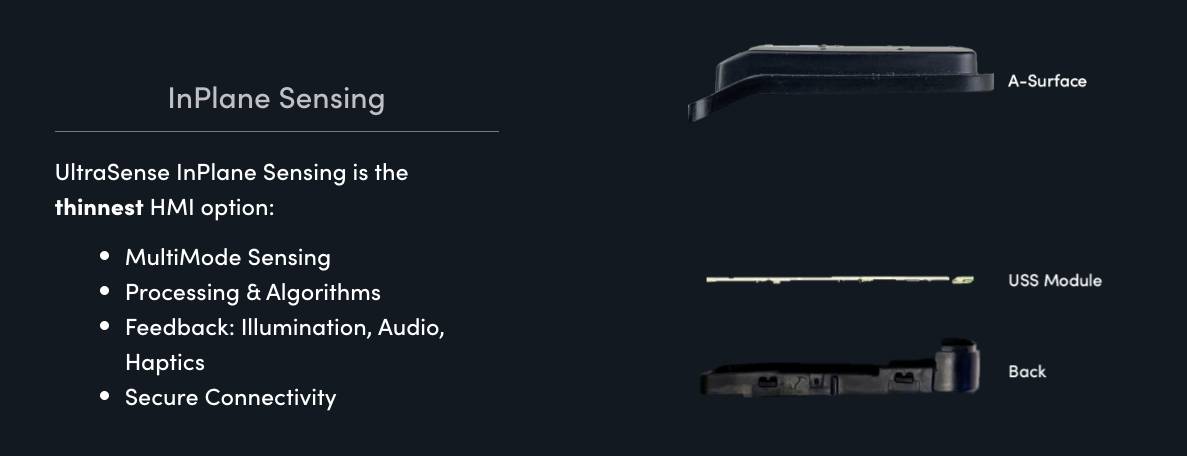
In the above figure the “USS Module” is the one InPlane sensing component and it laminates (though one of several methods to the OEM/Tier1s preference) and there’s an optional protective back that encases the module. Note this USS module is an extremely durable component that can also fit into other technologies such as InMold where the electronic component(s) are molded into the A-Surface.
Manufacturability
Manufacturing with fewer parts, and fewer complexities is a significant advantage, all relating to cost reductions and when using solid-state components compared to mechanical switches and multiple parts result in higher reliability, pleasing design aesthetics.
Supply Chain
The approach of manufacturing from a series of discrete components mentioned earlier also introduces the Supply Chain issue, that is that the assembly is not complete till all the discrete parts are available. It only takes one delayed part to stop production.
In comparison if there were only one component that could replace a set of discrete components then there are vast supply chain benefits, provided the part had high availability. Production time is also simplified because there are fewer components to assembly, and if the part offered optionality, the configurability to meet varying needs, one part for good, better, best offerings, it simplifies manufacturing.
The Merit of Truth
It all starts with great sensing. It’s the starting point that drives and enables good orchestration of the feedback effects, particularly necessary for great haptic feedback in solid-state designs. Great sensing is measured in accuracy, the goal to strive to hit 100% accuracy of intended touch and rejection of unintended touch. (See blog on the “Merit of Truth” Explained for more information.)
The most basic or common sensing is using a sensing technology such as capacitive. Many know there are challenges with using only one sensing technology as “the merit of truth.” the challenges with things like capacitive technology, in that its accuracy can be challenged with specific scenarios, sometimes called corner cases such as wearing gloves, or interactions with liquids like water drops can impact its sensing accuracy. There are several approaches to improved accuracy, two common approaches are multi-mode sensing, and algorithm logic (the highest forms are Artificial Intelligence, that include Machine Learning Algorithms). Using the appropriate approach is a function of the challenges that need to be solved and the effort and desire to achieve a given level of accuracy in both properly detecting an intended interaction and rejecting in advertent actions.
Closely tied to accurately sensing touch, the next dimension has several names, from accidental activation, false triggers, un-intended touch. These inadvertent actions manifest themselves in many ways but accidental activation avoidance is another critical measure that enhances the touch sensor’s score.
Multi-Mode Sensing
Multi-Mode for sensing is like the name implies uses several modes of sensing, sometimes described as “sensor fusion.” Traditionally the components of sensor fusion include multiple types of sensors, a Dual-Mode sensor uses two forms of sensing together.
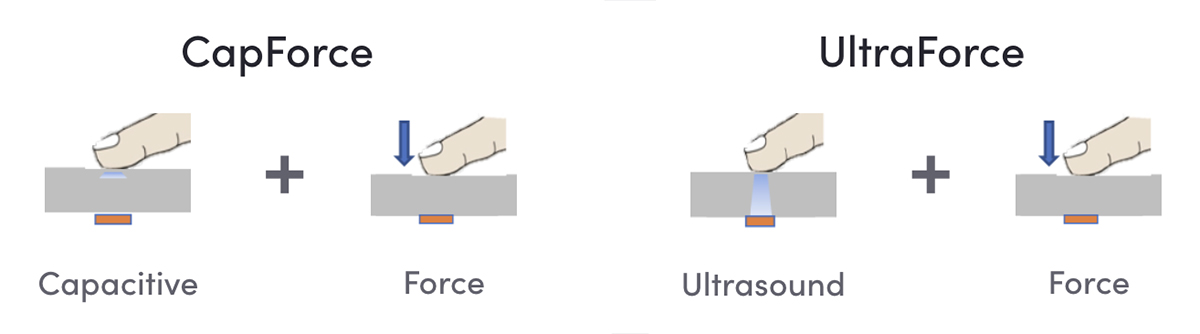
To include two forms of sensing it must be integrated in a processor with algorithms. Obviously the better faster the processing the better, but the need is to ensure zero latency. When shifting processing to a shared host could and often introduces latency. Note our measure of latency is not the best case, but the worst case, the scenarios of the processor under normal full use, and there should not be latency for good usability performance. The other way to resolve is to have dedicated local processing so it’s just focused on the HMI needs and isn’t bogged down with other tasks. (We will introduce more details on the topic of Zero Latency)
InPlane meets UltraSense SmartSurface HMI
The InPlane challenge is to find and assemble the right components to make it all happen. The UltraSense SmartSurface HMI is an excellent choice because its one tiny silicon component that is the size of the date printed on a penny, and it can deliver it all-in-one control capabilities.
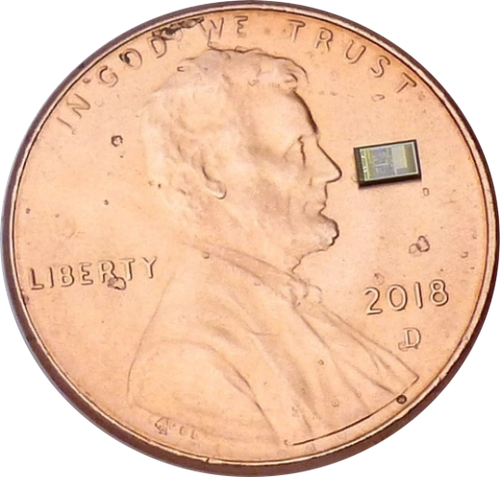
Rapid Prototype Development
When developing prototypes, depending on your companies’ capabilities, the SSI is ready to roll, inset into opening and connect to get started fast.
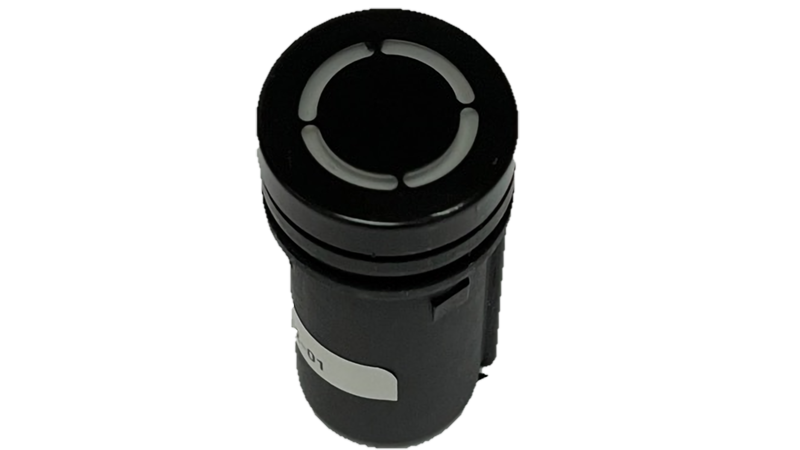
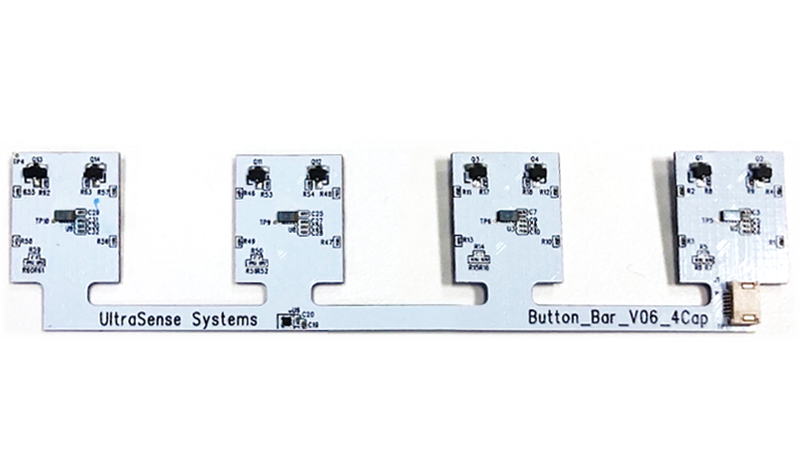
This is one of many modules available and has the capabilities with the component configuration*:
Sensing TPZ HMI controller, in CapForce Mode with Cap Sensing Layer,
Processing and Algorithms in TPZ controller
- 1st and 2nd Order algorithms for increased touch accuracy and elimination of accidental touch events
- Fix-In-Post tuning for better systems experience design
Feedback control:
- LED Illumination with PWM effects to attenuate and dim, as well as heartbeat and other effects,
- Audio control that can drive an additional internally located speaker or connect to a network addressable audio system,
- Haptics control that includes the driver to process custom pattern waveforms and with the ability to connect a haptic motor
Communications control: LIN protocol along with standard GPIO
*Note exact features are module specific and subject to change per module design
USS Modules exist to help rapid prototype solutions and are intended to laminate to the backside of the A-Surface.
InPlane Essential Requirements:
The key ingredients checklist to enable InPlane technology:
- Multi-Mode InPlane Sensing (Sensor Fusion)
- ML Algorithms for increased accuracy, and Fix-In-Post capability to enhance and tune design after the design prototype is built
- UX Design Tool (home grown or off the shelf) that can tune the experience, in the assembly, in the component (like in the steering wheel), and fully installed in the vehicle prototype
- Edge Processing to ensure low latency feedback, essential for experience based controls such as haptic feedback performance
- HMI Controller or a DiY controller board to combine all the key aspects in one InPlane module.
Note: The more components the higher the supply chain risk, the higher the coordination with multiple drivers and maintenance updates, an all-in-one solution helps deliver the full experience with one part.
- Optionality: which is the ability build one part and enable options via firmware/software settings. This simplifies manufacturing, supply chain and can reduce part numbers yet can easily be configured to support a good / better / best type of offering, and enabled at the factory build, at the dealership, or after sale through Over-The-Air (OTA) updates.
- Product development options include options of USS Solid State interfaces (SSI), or use existing HMI modules that help speed up prototyping, or develop custom HMI boards for serial production.
For select applications, the option to select an existing readily available SSI design could be the fastest prototyping method for creating the opening in the A-surface for adhering the SSI. SSI applications are pre-calibrated and ready to roll. SSI solutions are available in all shapes and sizes, including solutions for door, eLid and more.
Contact USS for more information
什么是InPlane
在汽车中,表面被定义为XY方向上的任何材料。这可能是仪表盘、中控台、内门、顶棚、方向盘的表面。横截面厚度的方向是Z。而从传感的角度来看,这被称为堆积厚度。用户接触到的表面通常被称为A-Surface。在一张塑料板上,A-Surface的厚度将是堆积厚度。在这个例子中为2毫米。
InPlane sensing是在物理上可能的最薄厚度里提供传感输入的能力,与A-Surface在同一平面,所以传感器在A-Surface的平面。
今日的传感器模块
今天的传感器模块需要支持传感层和控制器电路。在提供HMI(人机界面)体验时,还有反馈,可以包括几种类型的反馈,如照明、音频和触觉,或者是机械机制的机械反馈,如来自触觉开关的反馈。
在使用传统照明方法的汽车照明应用中,有一个光管框架,LED通过光管在一定距离内发出光线,以达到指定的亮度,为给定的图标提供背光。智能照明不仅照亮触摸点以告知什么功能被启用,而且当它被启用时,会显示不同的颜色以显示它被启用。
比如说:
不发光=隐藏/不可用的接触点。
白光=可用的发光触摸点(例如:车头灯白色图标,灯是关闭的)。
绿灯 = 启用的功能(例如:前照灯绿色图标,前照灯已打开)
蓝灯=次要功能(例如远光灯头灯蓝色图标,远光灯开启)
要了解如何在一个接触点上启用所有这些功能,请参考手势博客。 用户体验和最终行为与某些标准相联系,并在OEM的控制之下,它们取决于所选择的HMI设计组件的能力和界面设计师的想象力。有些人可能只需要白色来识别按钮,而不选择提供当前状态的反馈。 如果有多个接触点,可能需要单独解决每个接触点和其各自的功能。 并非所有市场上的技术/解决方案都能提供单个接触点的能力。
图1:传统HMI模块实例
传统的模块有几个功能部件
传感控制器(例如,电容式控制器,照明的反馈控制器)
处理控制器去控制传感器和反馈机制
反馈控制器PWM(脉冲宽度调制器)组件,用于
照明效果,(如调光或效果模式)
音频扬声器组件(例如在方向盘中)
触觉控制器和触觉马达(如果是固态元件)
通信模组,支持通过LIN或CAN等通用协议与汽车的其他部分连接。
例如,电容技术有一个传感层,使用的材料包括ITO(氧化铟锡)薄膜、FPC柔性印刷电路或PCB(印刷电路板),它提供了电容轨迹,与 A-surface压在一起,并与传感器硅连接,后者是一个带有支持电子元件的模块的一部分。
今天,最常见的汽车应用是这种传感膜层被贴在 A-surface的背面,并在少数情况下插入InMold,即成型部件中。
IME,模内电子是InPlane的一种形式,不仅是薄膜,而且包括控制器在内的整个传感电子元件都在成型件中。
InPlane的价值主张是,它在许多领域带来了惊人的效果,现在可以在 A-surface的平面上提供这种效果。
以一个现有的模块为例,确切的模块和制造商是不相关的,同样,确切的测量数字也是相对的,每个零件都会有不同,但在这个生产HMI零件装配的拆解分析中,与InPlane的薄度比较是不能忽视的。 塑料量的减少带来可持续性和可回收性的优势。 总的空间,体积腔体大幅减少,使设计师能够在以前不可能的地方创造互动。
想象一下,一个中控台储物箱盖,InPlane可以适用于传统组件甚至不能考虑的地方,使新的应用成为以前没有的选择。 当在整个车辆上实施时,就像在汽车布线中一样,网络协议可以大大减轻重量,就像过渡到网络化布线一样,这提供了同样的重量节省,增加了驾驶里程,这最终是一个击中汽车买家底线的措施。
InPlane是一个单一的平面薄模块,也可以成为传感以外的其他所需组件的表面,如MCU、反馈,可能包括照明、扬声器或触觉电机和通信板。
InPlane传感人机界面是提供所有组件的能力,主要传感、处理、反馈、通信都在 "平面内"。
用InPlane重新想象
现在重新想象一下过去用当今先进技术能力所做的事情。原始设备制造商可以重新思考过去的方式,并在更小的空间内获得同样的好处。随着关键部件的整合,可以集成到一个(些)微小的部件中,这现在正在成为现实。 平面传感和平面人机界面(传感加集成控制、处理、反馈和通信)是OEM(和Tier1s)提供这种新体验的方法。
在上图中,"USS模块 "是一个InPlane传感组件,它是层压的(尽管是OEM/Tier1s偏好的几种方法之一),有一个可选的保护性背面,将模块包裹起来。 请注意,这个USS模块是一个非常耐用的组件,也可以适用于其他技术,如InMold,其中电子元件被塑造成A-Surface。
可制造性
用更少的部件和更少的复杂性进行制造是一个显著的优势,所有这些都与降低成本有关,而且与机械开关和多个部件相比,使用固态元件会带来更高的可靠性,以及令人愉悦的设计美学。
供应链
前面提到的从一系列离散部件开始制造的方法也引入了供应链的问题,即在所有的离散部件可用之前,装配是不完整的。只需要一个延迟的部件就可以停止生产。
相比之下,如果只有一个部件可以取代一组离散部件,那么就会有巨大的供应链利益,只要该部件具有高可用性。 生产时间也得到了简化,因为需要组装的部件较少,而且如果该部件提供了可选性,可配置性以满足不同的需求,一个部件就能提供好的、更好的、最好的产品,这就简化了制造。
真实性的优点
这一切都从伟大的传感开始。 它是推动和实现反馈效果的良好协调的起点,特别是对固态设计中伟大的触觉反馈是必要的。伟大的传感是以精确度来衡量的,目标是努力达到100%的预期触摸精确度和拒绝非预期触摸。 (更多信息请见博客 "真理的优点 "解释)。
最基本或最常见的传感是使用电容式等传感技术。 许多人都知道,只使用一种传感技术作为 "真理的优点 "是有挑战的。像电容技术这样的东西,其准确性会受到特定场景的挑战,有时被称为角落案例,如戴手套,或与水滴等液体的相互作用会影响其传感准确性。 有几种方法可以提高精确度,两种常见的方法是多模式传感和算法逻辑(最高形式是人工智能,包括机器学习算法)。 使用适当的方法去提供高准确性的互动增加精度,降低误触。
与准确感知触摸密切相关的下一个维度有几个名称:意外激活、错误触发、非故意触摸。 这些误触行为有多种表现形式,但避免意外激活是提高触摸传感器分数的另一个关键措施。
多模式感应
多模式传感就像它的名字一样,使用几种传感模式,有时被称为 "传感器融合"。 传统上,传感器融合的组成部分包括多种类型的传感器,双模式传感器同时使用两种形式的感应。
图3:双模式传感的例子
为了包括两种形式的传感,它必须被集成在一个带有算法的处理器中。显然,处理速度越快越好,但需要的是确保零延迟。当把处理转移到一个共享主机上时,可能而且经常会引入延迟。注意我们对延迟的衡量不是最好的情况,而是最坏的情况,即处理器在正常充分使用的情况下,不应该有延迟以获得良好的可用性能。另一种解决方法是有专门的本地处理,这样它就只专注于HMI的需求,而不被其他任务所困扰。(我们将介绍更多关于零延迟主题的细节)
InPlane与UltraSense SmartSurface HMI相遇
InPlane的挑战是找到并组装合适的组件来实现这一切。UltraSense SmartSurface HMI是一个很好的选择,因为它的一个微小的硅元件,只有一分钱上印的日期那么大,它可以提供它所有的控制能力。
图X 。USS TouchPoint Z人机界面控制器
快速原型开发
在开发原型时,根据你公司的能力,SSI已经准备好了,插入开口并连接,可以快速启动。
图x: USS固态接口
图X: USS样本TouchPoint Bar Module
这是众多模块中的一个,具有组件配置的能力*。
感应TPZ人机界面控制器,在CapForce模式下有Cap Sensing Layer。
TPZ控制器的处理和算法
一阶和二阶算法,提高触摸精度,消除意外的触摸事件
Fix-In-Post调整,用于更好的系统体验设计
反馈控制
带有PWM效果的LED照明,可以减弱和变暗,以及心跳和其他效果。
音频控制,可以驱动一个额外的内部位置的扬声器,或连接到一个网络可寻址的音频系统。
触觉控制,包括处理自定义模式波形的驱动器,并能连接触觉电机。
通信控制:LIN协议和标准GPIO
*注意确切的功能是针对模块的,并可根据模块的设计而改变。
USS模块的存在是为了帮助快速的原型解决方案,并打算贴在A-Surface的背面。
InPlane基本要求:
启用InPlane技术的关键成分检查表:
多模式平面内传感(传感器融合)
用于提高精确度的ML算法,以及在设计原型建立后加强和调整设计的Fix-In-Post能力
用户体验设计工具(自制的或现成的),可以在装配、部件(如方向盘)中调整体验,并完全安装在车辆原型中。
边缘处理以确保低延迟反馈,这对基于体验的控制(如触觉反馈性能)至关重要
人机界面控制器或DiY控制器板,将所有的关键方面结合在一个InPlane模块中。
注意:组件越多,供应链风险越高,与多个驱动程序和维护更新的协调也越高,一个一体化的解决方案有助于用一个部件提供完整的体验。
可选性:这是建立一个部件并通过固件/软件设置启用选项的能力。这简化了制造和供应链,可以减少零件数量,但可以很容易地进行配置,以支持好/更好/最好的产品类型,并在工厂制造、经销商处或售后通过空中(OTA)更新启用。
产品开发选项包括USS固态接口(SSI),或使用现有的人机界面模块,以帮助加快原型设计,或开发用于批量生产的定制人机界面板。
对于选定的应用,选择现有的现成的SSI设计可能是最快的原型设计方法,用于在A-Surface创建开口以粘附SSI。SSI的应用是预先校准并准备好的。 SSI解决方案有各种形状和尺寸,包括门、eLid等的解决方案。
联系USS获取更多信息